How to grade the quality of surgical instruments?
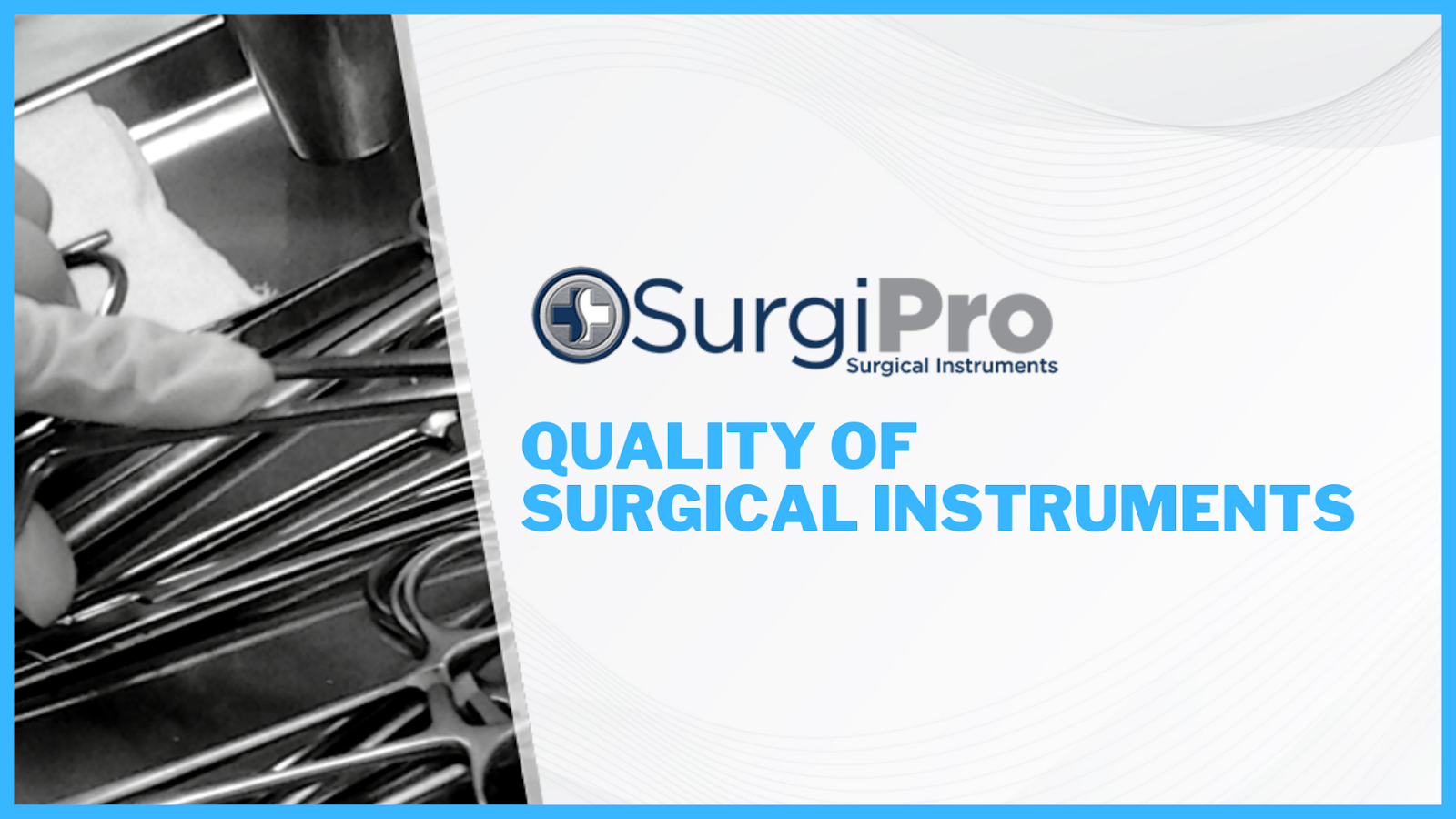
Criteria for evaluation of surgical instruments are: materials, craftsmanship, and quality control are all considered when evaluating an instrument’s overall quality and grade. In 2012, almost 100,000 accounted for surgical technicians in the United States with 15% increase by 2024. Their main focus is on patient safety and surgical supply management to guarantee a successful treatment. With 30-plus years of experience, this article will help you to prep and arrange surgical instruments correctly in the operation room.
Master Craftsmen checks every step of the manufacturing process, conducting stringent quality control along the way. Professional Instruments uses German stainless steel 400 series in manufacturing. To avoid glare from surgical lights, premium equipment usually has a matte or satin surface. Superior quality ensures a piece of precise, corrosion-resistant equipment that, if properly cared for, will last the surgeon for many years. Premium equipment usually comes with extensive manufacturer’s warranties.
Top Instruments are likewise made of the German Stainless Steel 400 series, although they are often completed outside of Germany and subjected to less stringent quality controls. A matte or satin finish is also possible on mid-grade instruments. The mid-grade quality instruments do not offer warranty and also get at a cheaper price. Instruments made with 400 Series Stainless Steel from a variety of suppliers are likely to rust and corrode quickly. Due to only few check during manufacturing of these surgical instruments reduces it’s quality and standard. Economy instruments usually have a gleaming finish and are less expensive to replace than to service.
What is the process to make surgical instruments?
Stainless steel is used in the majority of surgical equipment, but other materials like titanium, silver, and heavier metals like Tungsten Carbide are also used. In manufacturing of surgical instruments. The stainless steel grades that are commonly utilized include 400 and 300.
Even though stainless steel is generally corrosion-resistant, it is nonetheless susceptible to rust and corrosion. Perhaps a preferable term to avoid this misunderstanding is stain-resistant, rather than stainless or stain-free.’ This is due to the fact that stainless steel can be corroded by a variety of factors. High acid or alkaline concentrated detergent, friction with other non-corrosion resistant metals (during or after manufacturing), flaws in steel, lubricating electrolytes, high chloride conditions, and other factors are among them. However, corrosion can be avoided with good material and tool selection, manufacturing care and processes such as passivation, and proper pre-and post-use care and handling in hospitals.
How to Prevent Surgical Instruments from Spotting, Staining, and Corrosion?
Spotting, staining, and corrosion of surgical instruments are important issues in many hospitals. These issues can be avoided if the manner of processing the instruments is carefully considered and possible causes are identified. This article discusses why it’s important to keep an eye on the instrument-processing scheme, as well as the basics of instrument creation. Symptoms of issues are described, as well as descriptions of frequent causes of instrument malfunctions.
On the market, there are thousands of various types of surgical instruments. Stainless steel makes up the great majority of these instruments. Hardened inlays are found in some of these instruments, which are usually recognizable by their gold handles. The composition changes depending on the intended application. A cutting edge, for example, would be constructed of a softer steel than a grabbing device. The 300 series stainless steel sheets are typically the tougher stainless steel. The 400 series stainless sheets of steel are gentler stainless steel, such as those used in surgical blades. The materials used in the 300 series are more corrosion-resistant.
How do you sterilize surgical instruments for the best use of them?
While this may appear to be a little step, it is crucial. Prior to usage, surgical tools must be sterilized. Outside the package, a chemical indication should be placed. If the pack has been exposed to the sterilization procedure, it will change color. This does not, however, imply that the objects are sterile. In order for the package to fulfill the necessary Sterility Assurance Level (SAL) and be considered sterile, a chemical indicator or integrator must be altered inside of it. If the integrator is absent or has not changed color, the package should be regarded as unsterile and should not be utilized. All other things on the table will be considered contaminated if an unsterile set is placed on the sterile back table.
Hopefully, this article has given you a better understanding of the various types of metal used in surgical equipment, as well as their qualities.
As you can see, stainless steel is the most common material since it is relatively inexpensive, abundant, and suitable for most uses.
Titanium is the next most popular material because it has more strength and can easily bond with the bone, making it suitable for orthopedic implants.
The characteristics of tantalum make it an excellent material for surgical equipment.
Finally, valuable metals such as platinum and palladium exist. These are the most expensive, which is why they’re rarely used in medical settings, but they’re perfect for small, precise instruments and parts.
Last but not least, increased demand is driving the development of new cost-effective production technologies. This aids in increasing production output without sacrificing product quality.
Conclusion
Surgical instrument repair and surgical instrument repairs are critical to the quality. Proper repairing and sharpening of surgical instruments insure longer life of these medical tools. Performance if the surgical instruments are crucial. Proper repairing and sharpening of surgical instruments insures quality and durability. Some surgical instruments like foreceps and need repairing and sharpening after specific time to maintain quality and performance. We have highly trained surgical instruments repair specialist at Surgipro. The specialist stay up with latest technologies through ongoing education and different training programs. Repairing service reduces operating costs of your medical facility. It also improve the life of your surgical instruments.
There are hundred of ways these surgical instruments can help you. To learn more about call us at 877-252-5865. at Surgipro specializes in refurbished and German surgical instruments. To learn more about how the services can benefit you and your patients, contact at surgipro@surgipro.com.