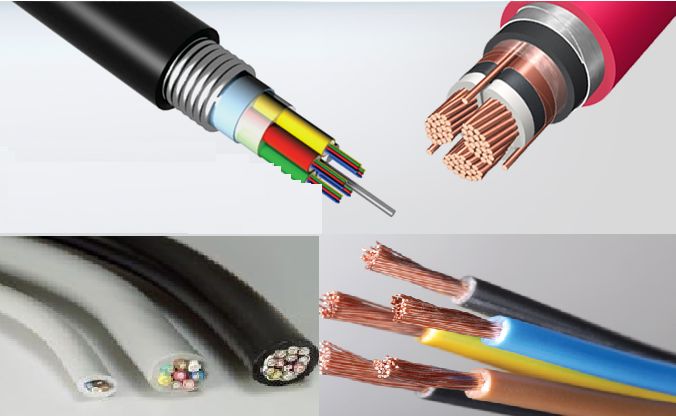
If you have ever wondered what the difference is between BV and BVR electrical copper wire manufacturers, you are not alone. This article will help you understand the difference between the two types of electrical wire and what each one is used for. In addition, you’ll learn about the processes used in copper wire manufacturing and the applications for which it is used. Then, you can decide which one you want to purchase. Let’s get started!
Copper wires are similar, but they are designed for different purposes. BV wire is a hard single-strand copper wire, while BVR wire has multiple conductors with a soft insulation layer. Both types are commonly used, and they are suitable for wall penetration, but they are not designed for tube turns. BV wires are available in common colors like red, green, and yellow, but they are not as flexible as BVR. BVR wire is composed of multiple thin and thick copper wires that are made to resist twisting and bending.
The diameter of the core is different between BVR and RV wires, but they share the same operating temperature. A Best electrical wire company has a maximum operating temperature of 70deg C, while an RV wire has a maximum working temperature of 80deg C. If you need high temperature resistant electrical copper wire, however, it’s best to choose the BVR type. You’ll be pleased with the results.
There are several processes used to manufacture copper wire, including drawing, electroplating, and coating. Copper wire is drawn into strands by two separate processes. The drawing process is followed by an annealing step. During this process, copper wire is heated to around 1000-1200 degrees Fahrenheit, which relieves internal stresses and softens the surface of the metal. The wire then undergoes a cooling process before moving to the next manufacturing stage.
Processes Used to Manufacture Copper Wire:
Once a coil is made, it is transferred by an overhead crane to an insulating line. One coil can feed the insulating line for two days. The insulate line performs several functions, including reducing the copper wire size. Diamond dies are used to cut the copper wire. Once this process is complete, the copper wire is ready for further drawing and finishing. Here are the processes used to manufacture copper wire:
Conventional copper wire manufacturing requires a great deal of energy. The capital and labor costs are significant. Moreover, the product is subject to oxidation and contamination. Foreign materials, such as metal dust, may damage wire drawers and cause the wire to break during drawing. In addition, this process involves extensive toxicity. Further, the wire is susceptible to breakage when it reaches the hands of the end user.
Copper is a great conductor of electricity and can be used to create numerous alloys. Beryllium copper wire is one such alloy, with a copper core coated in a steel shell. These alloys are great for many applications, including motors, power supplies, and medical products. In addition, these wires are highly flexible and nonmagnetic. As an alloy, copper can be combined with other metals to increase desirable characteristics, such as strength, solderability, and conductivity, while reducing weight.
Why is Copper Used in Electrical Appliances?
Another type of copper wire is braided. These wires can resist high temperatures and corrosion caused by a salty medium, and are particularly useful in marine units and submerged generators. Copper wire braiding is incredibly durable and flexible, and can be coiled into very small diameters for a number of applications. In addition to electrical applications, copper braided wire is great for coating other wires, such as hoses.
If you are searching for copper wire manufacturers, you must be familiar with these four basic features: metal, strength, and conductivity. The quality of the wires depends on these factors, which are important for every application. However, you must know that these wires don’t necessarily have to be the most expensive. The top manufacturers of electrical wires follow strict standards, and provide export-quality wire packaging. For example, they adhere to the PT4 & PT10 standards and also follow the DIN standards.
The manufacturing process for copper wire requires a specific set of processes. The process of annealing involves heating the wire to a temperature that relieves internal stresses and softens the surface of the metal. The wire is heated to a temperature between 1000 and 1200F, then cooled in water to remove excess heat and minimize the risk of oxidation. The final product is usually red or turquoise in color. There are many uses for copper wire in today’s market, including electrical and electronic devices.
Is Fibre made of Copper Cables?
The process of drawing wire strands involves successively smaller dies, with the size of the wire increasing as the strands are drawn. To size the wire, single core cable price in Pakistan sizing system, where a smaller wire passes through fewer dies. Copper wire is a standard electrical conductor. It is ideal for pressure terminations. Hence, manufacturers use diamond dies in their manufacturing process.
Copper is a highly conductive metal. Its properties have made it a common material for electrical wires and connections. In 1913, copper became an international standard, and its conductivity is now 100 percent IACS. Processing technology has changed, but copper’s inherent characteristics remain the same: high tensile strength, good thermal conductivity, and excellent electrical conductivity. The ASTM B3 specification specifies copper wire that has been annealed and passes this test.
When comparing copper conductivity, it’s important to remember that not all conductive metals are created equal. The same is true of insulators. Not all metals are equally resistant to electron motion, and some change their electrical properties when subjected to different temperatures and conditions. Copper, on the other hand, is the most common conductor material. Its high thermal and electrical conductivity, ductility, and malleability make it a popular choice for many applications. Copper wire manufacturers need to understand the differences between the different types of copper for each application.
Mechanical Features & Specification:
There are many applications of copper wire, including power generation, transmission, and telecommunications. Copper is also found in many appliances, including televisions and refrigerators. In order to get the most value for your money, you need to purchase the best quality electrical copper wire. Manufacturers of this metal should have a strong commitment to purity, and should never compromise that quality in the production process. Copper wire has the following properties:
Good corrosion resistance and other mechanical properties make copper a top choice for the electrical industry. Quality wires from leading electrical copper wire manufacturers offer excellent value throughout their product’s lifecycle. Choosing the best wire supplier for your needs will ensure a reliable product that can last for years. Copper wire has many benefits over other materials, including low reactivity. And it is much less likely to experience a short-circuit during installation.
Mechanical features of electrical copper wire manufacturers can be identified based on the thickness of the oxide film on the surface of the material. This film forms during the drawing process and often exhibits the characteristics of a die mark. This film can also appear as a sliver or gouge, indicating a defect. Its presence can be detrimental because it may cause defects during the drawing process, causing excessive wear on drawing dies, as well as a poor adhesion of the enamel film to the bare conductor.
Best Ethernet Cables:
Electrical wires with robust mechanical features are essential for effective performance. Make sure that you buy copper wires with certifications from domestic as well as international bodies. Also, make sure that the copper wire you buy meets the requirements for the type of application you are going to use it for. Make sure to ask questions if you are unsure of its usability, and find a supplier who can provide the right kind of products.
When buying electrical copper wire, it is important to check the manufacturer’s technical specifications. These should include tensile strength, elongation and resistivity. Micrometer calipers with a vernier are used to measure dimensions. Lastly, the wire should meet particular requirements for surface finish and size. Purchasing the wires from a reputed manufacturer should be hassle-free and provide maximum value for money.
A variety of technical specifications are available for different types of conductors. For example, the American Wire Gauge specifies the physical size of copper and aluminum wire. Smaller diameters are solid wire, while thicker diameters are stranded for flexibility. The other specifications of the wire are the TC cable, the underground feeder, and the mineral insulated cables. This article explores the technical specifications of electrical copper wire manufacturers, which can be found on the website of the wire manufacturers.
Conclusion:
A leading copper wire manufacturer focuses on continuous evolution and improvement. Their product portfolio is an indicator of their level of expertise and commitment to continuous improvement. Look for a manufacturer whose products cover the renewable energy sector. For example, a company offering PV ribbons and bus bars, winding wires for wind turbines, and electric vehicle wiring solutions should focus on this market segment. They should be a one-stop-shop for electrical wire needs.